Service
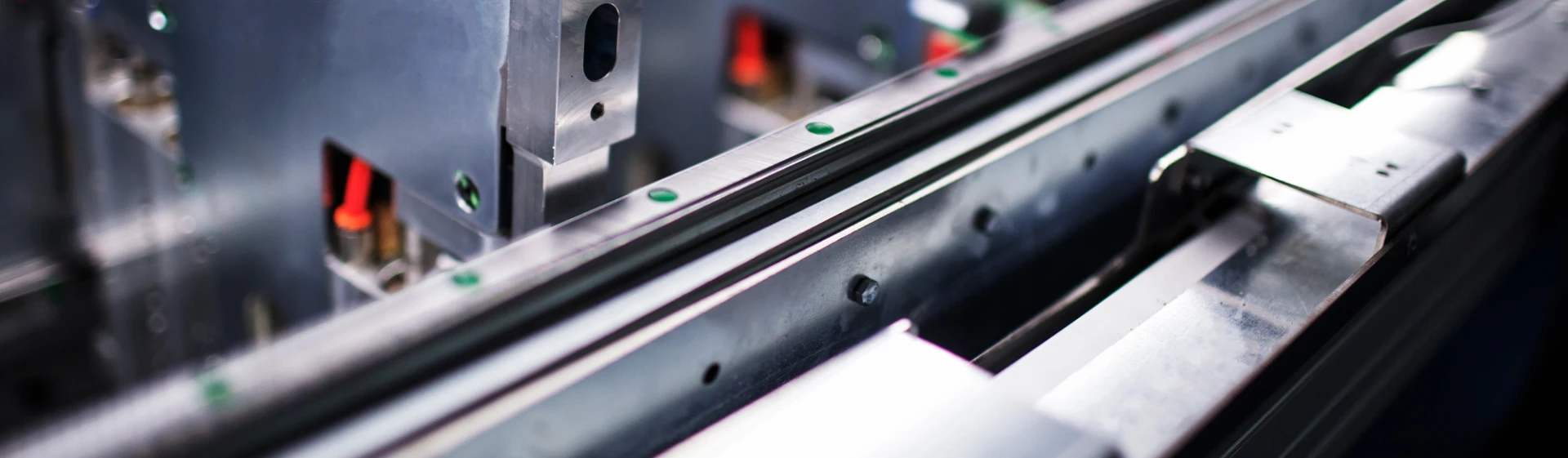
Service and spare parts
just a click away
At PANOTEC, we are committed to offering fast and effective after-sales support to our customers.
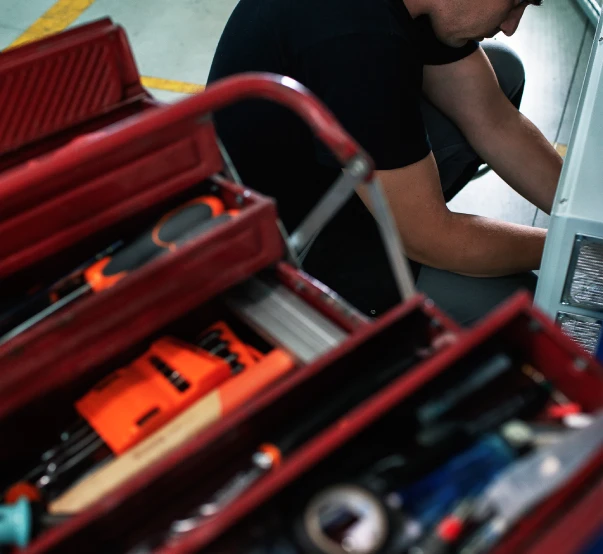
Our dedicated team is ready to assist you at every stage of using our equipment, ensuring a smooth operational flow and maximising your productivity.
Contact us now!
Monday - Friday from 8:30 am to 6:00 pm
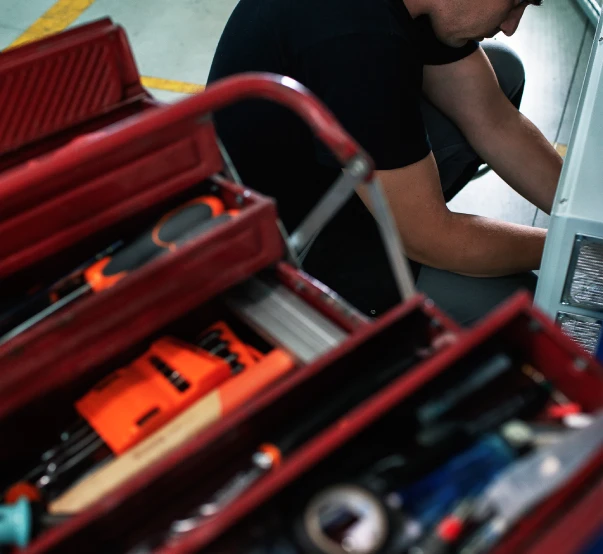
Do you need
immediate assistance?
Our ticket-opening system simplifies the reporting process and allows us to intervene promptly. Fill in the online form to open a support ticket and our team will get to work immediately to solve the problem.
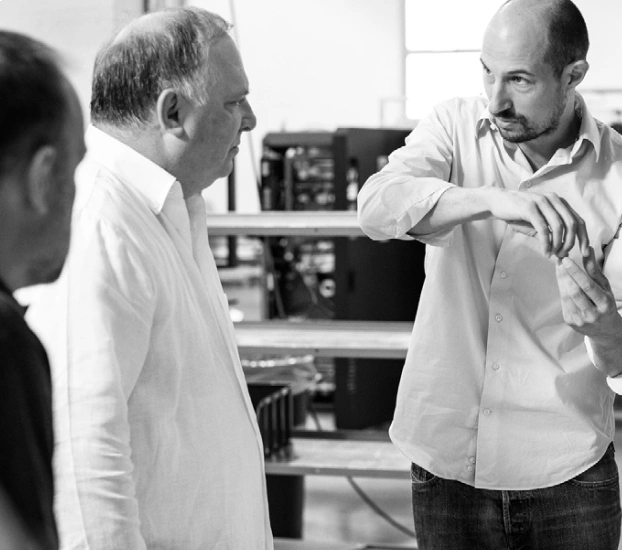
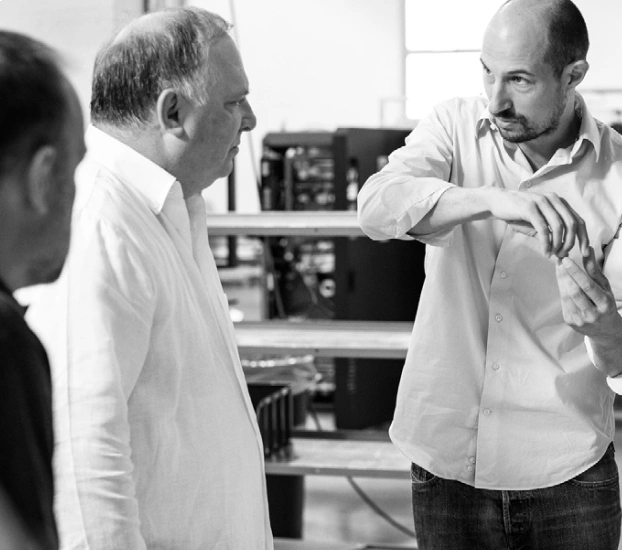
Our service
contracts
We are committed to ensuring the maximum efficiency and functionality of your systems by offering a comprehensive support and service contract. Evaluate the contract that best suits your needs!
EASY
REMOTE SUPPORT 8 AM-6 PM
ACCESS TO CUSTOMER AREA
-
-
-
Plus
REMOTE SUPPORT 8 AM-6 PM
ACCESS TO CUSTOMER AREA
1 FREE SERVICING OPERATION
SPAREPARTS: discount 7%
-
Pro
REMOTE SUPPORT 8 AM-8 PM
ACCESS TO CUSTOMER AREA
2 FREE SERVICING OPERATION
SPAREPARTS: discount 10%
PREDICTIVE MAINTENANCE
Smart | Plus | Pro | |
REMOTE SUPPORT | 08 - 18 | 08 - 18 | 08 - 20 |
CUSTOMER AREA | |||
FREE SERVICING OPERATION | - | 1 | 2 |
SPAREPARTS: discount | - | 7% | 10% |
PREDICTIVE MAINTENANCE | - | - |
FAQ
How can I contact a service technician?
To contact a Panotec technician for service, simply open a Ticket in the Jupiter portal.
How do I request a spare parts offer or ask for a technician?
You can contact the spare parts department by opening a ticket in the portal or by writing directly to spareparts@panotec.it
Where can I find the serial number of my machine?
The nameplate with the Panotec machine number is located on the right-hand side of the cardboard feeder.
How can spare parts and maintenance work be optimally managed?
One of our most important services is predictive maintenance, a procedure that allows us to anticipate and prevent potential breakdowns or operational problems by remotely monitoring the state of wear of machines and their components. Thanks to this technology, we are able to provide proactive service to our customers, keeping them informed of the status of their equipment and planning necessary maintenance activities together with them. With predictive maintenance, we can optimise operational efficiency and ensure greater machine reliability, minimising downtime and unplanned maintenance costs.