Evo
The packaging machine Evo is the product of more than 30 years of experience by our technical, electrical and software team and is one of the leading representatives of innovation in customised packaging.
Designed with the aim of combining flexibility and productivity requirements across a wide range of sizes, Evo is an highly efficient packaging machine for the automatic production of customized boxes.
Suitable for:
- Medium to large-sized companies
- Medium-high productivity requirements
- More than 6 boxes per minute
- Production in batches or in high flexibility (batch size 1)
- Numerous production sectors from furniture to e-commerce, from shower cubicles and automotive to digital printing
Find out how Evo can make your packaging process even more flexible!
Suitable for:
- Medium to large-sized companies
- Medium-high productivity requirements
- More than 6 boxes per minute
- Production in batches or in high flexibility (batch size 1)
- Numerous production sectors from furniture to e-commerce, from shower cubicles and automotive to digital printing
Find out how Evo can make your packaging process even more flexible!
Work phases
Entry of box pattern and dimensions
Available in manual or automatic version (CSV file or link to management system)
Box cutting and creasing in seconds
The packaging machine automatically selects the best available cardboard to create the optimised box, minimising waste.
Customised product packaging
MANUAL VERSION:
the operator manually packs products into customised boxes
AUTOMATIC VERSION:
automates your packaging area even more with our accessories
Features
Cardboard feeding
The packaging machines is fed by a continuous sheet of corrugated cardboard folded like a fan, known as a fanfold. If more than one fanfold slot is present, the machine automatically selects the most suitable cardboard width to optimise consumption.
Optional
Serrated creasing
Creasing with perforation in addition to Standard creasing: makes it easier for the operator to fold the cardboard, which also enhances its appearance.
Trim extraction and conveyors
Composed of:
- extractor to remove cardboard trim laterally
- conveyor belt to remove waste
End of cardboard sensors
A set of photocells that give an early warning that the cardboard pallet is running out.
Double driver
Implementation of a 2nd automatic longitudinal positioning unit, resulting in a reduction of repositioning time by up to 40%.
Box code printing management
Integrated solution for printing codes, short descriptions or barcodes on the inner surface of the box by means of ink-jet marking with 12.7 mm HP print head.
Label printing management
Integrated label printing solution in combination with box production with network-connected thermal transfer printer.
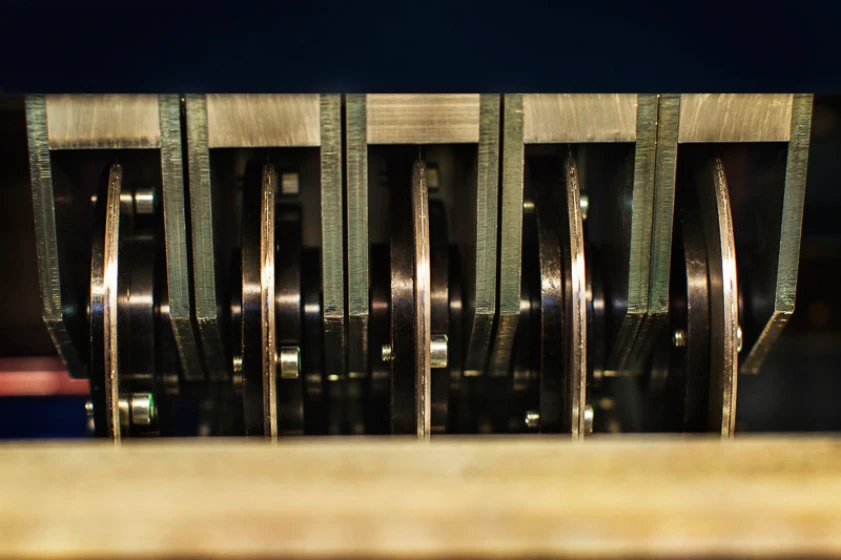
Technical
data
Machine width/span
2.5
Productivity level
medium / high
Boxes / min
over 6 / min
Boxes / day (batch production 1)
1000 - 1500
Boxes / day (in batches)
2000 - 2500
Cardboard feeding rate
45m / min
Cardboard feeding type
fanfold / sheets
Number of cardboard cassettes
up to 12 fanfolds
No. longitudinal cutting and creasing units
up to 12
Normal / serrated creasing
Normal / serrated
Cardboard trim management
available
Cardboard thickness
2 mm to 7 mm
Software
included
Interested?
Write us to request more information
(Required fields marked with *)