In the automotive industry, high-quality packaging is essential to ensure that components reach their destination without damage. Companies manufacturing components for this sector require cardboard packaging that is both highly durable and tailored to specific formats and features. Panotec addresses these requirements with machinery capable of producing over 40 different box formats, customized to the desired size. With advanced, flexible technology, custom cardboard boxes can be produced on-site directly from fanfold cardboard, optimizing production and lowering operational costs. In this article, we will examine an example of a highly automated plant by looking at the Denso client case study.
Denso case study: A Highly Automated Packaging Plant
When Denso turned to Panotec, they had the following objectives:
- Make the packaging process more efficient, which was previously done entirely manually.
- Achieve a planned ROI of five years.
- Drastically reduce the number of oversized boxes to optimize warehouse and shipping volumes.
- Increase current productivity from 600 pieces per day.
- Maintain the excellent quality of the packaging.
Thanks to a highly automated plant for producing custom-made boxes, it was able to:
- A highly automated plant was designed. The only manual procedure is inserting the product into the box; due to its particular nature, it needs to be handled with great care.
- Achieve an actual ROI in less than two and a half years.
- From 26 box codes to be manually adjusted, the plant can produce and manage 2,307 different box sizes.
- To maintain packaging quality, the plant is equipped with two packaging machines: one dedicated to producing and forming the tray that contains the product to be packaged, and the other to produce the external packaging. This ensures perfect protection of the product inside, and the custom design for the client has maintained good aesthetic quality.
The automated system manages the production of trays, the forming and closing of customized packaging, and a station dedicated to the manual insertion of the product into the tray, with its terminal and manual scanner for managing dimensional changes of the working batches. This plant has allowed Denso to manage over 2,300 different box sizes, drastically optimizing the box warehouse, replaced by a small number of fanfold pallets.
A detailed example of a system capable of precisely and automatically managing the production of bases and lids can be found at the following link: Panotec Bottoms and Lids Systems.
Denso Packaging Flow
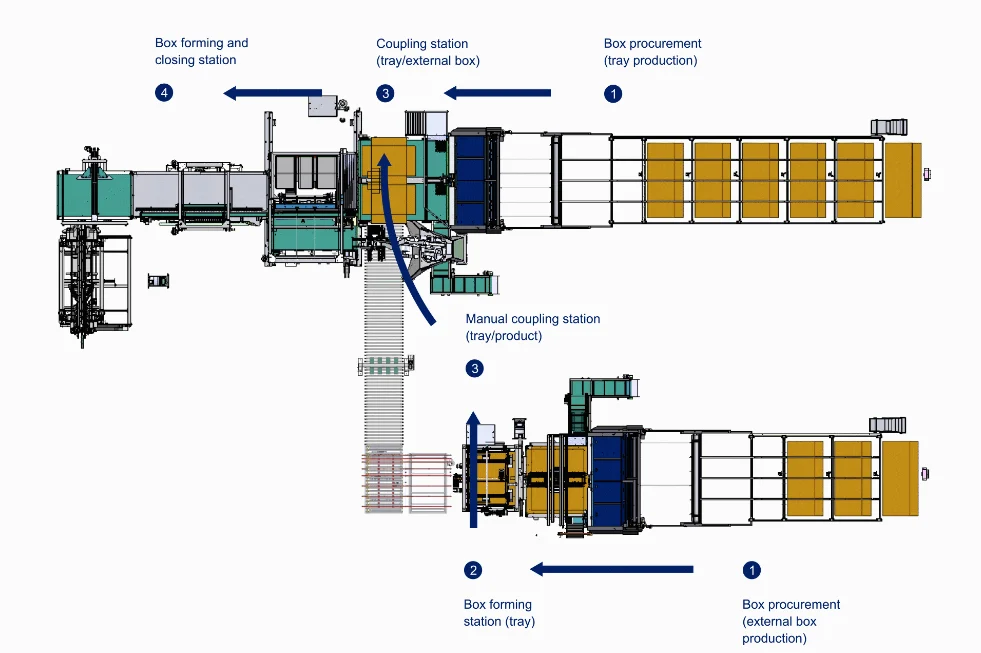