In this article, we present our packaging solution for the furniture sector, specifically for assembled furniture, illustrated through the successful experience of one of our clients: Pianca.
In the furniture industry, effective packaging is crucial to ensure that furniture arrives at the customer in perfect condition. Furniture companies that produce assembled pieces usually need American boxes, which come in various sizes and are equipped with protections for safe transport.
By using continuous cardboard as a raw material, the machinery produced by Panotec is capable of creating boxes and protections of various types and sizes with complete flexibility and as needed. In this scenario, customized packaging solutions become a key element. They allow companies to eliminate the use of plastic filler materials, minimize material waste, and provide an exceptional customer experience, further reinforcing their commitment to sustainability.
One client who has embraced this vision is Pianca, a renowned company in the high-quality furniture sector. In this article, we will explore their successful case.
Pianca Case Study: A Highly Automated Packaging System
The customer approached us because they were pursuing the following goals in order to enhance their production flow:
1. to increase the productivity of the packaging assembly line, which so far had been handled in a totally manual way.
2. to reduce materials that are harmful for the environment such as polystyrene protections (applied BY HAND and not recyclable)
3. to cut down deviations and waste (according to the concepts of MUDA & MURA) to a minimum in order to save time and manage consumption in efficient ways
4. to reduce returns to a minimum
5. to improve the appeal of the packaging and therefore the product image since customer’s associate a high quality packaging with a high quality product
In order to meet the customer’s needs the following solution was implemented:
1. Panotec provided a fully customized and fully automated system to produce and close fefco type 201 boxes.
2. All the polystyrene protections were replaced by honeycomb cardboard blocks applied automatically on all 4 sides of the box.
3. By implementing this solution along with the production of a tailor-made box just-in-time, thus reducing the amount of time allocated for packaging operations, productivity increased significantly (35”/box).
4. The box is provided with an additional protection and returns due to transport damage were significantly reduced from 12 to only 1 per month.
5. Effective improvements could be achieved in terms of product image (a high quality box for a high-quality product) and operational requirements (storage, handling and transport protection).
Pianca’s challenge was to meet market and customer demands while maintaining a strong commitment to eco-friendly production. To address this need, Panotec developed a completely customized and automated system for the flexible production and sealing of a wide range of box sizes. With Panotec’s collaboration, traditional polystyrene protections were completely eliminated and replaced by a section dedicated to the automatic application of corrugated cardboard blocks on the four sides of the box. This solution provided the boxes with an additional layer of protection, drastically reducing the risk of damage during transport. The result was impressive: returns were reduced from 12 to 1 per month.
In conclusion, the combination of operational efficiency and environmental sustainability demonstrated the value of the collaboration between Panotec and Pianca. For more information on the system, read: American Boxes Packaging System
Pianca Packaging Flow
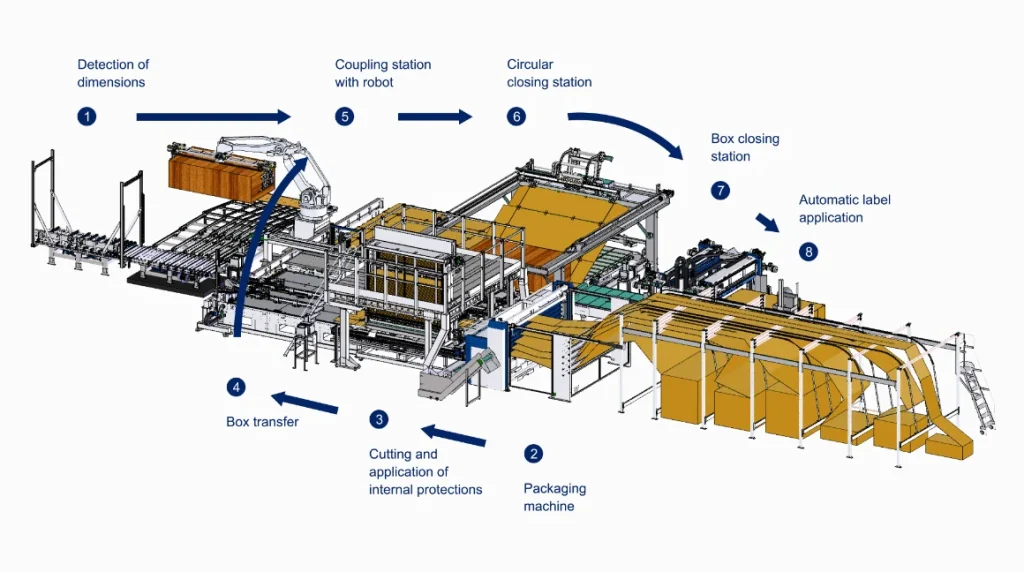